Así se puso Seat a fabricar un respirador
Cada OxyGEN tarda entre 40 y 50 minutos en salir de la línea de ensamblaje, lo hacen 150 empleados, repartidos en dos turnos de diez horas
La doctora Patricia Such y el ingeniero David García probablemente solo se ven una vez al año, coincidiendo con las revisiones médicas de Seat en Martorell. O puede que ni eso. Sin embargo, la crisis del coronavirus, ha convertido sus encuentros en habituales, diarios. Los dos forman parte del engranaje que la empresa automovilística ha puesto en marcha para contribuir a la batalla contra el COVID-19.
Ambos son piezas esenciales en el desarrollo final de los respiradores OxyGEN que se producen en la línea 1 del Taller 9 de la planta de Martorell. Tan piezas esenciales como los 30 empleados voluntarios que en cada turno (hay dos de momento) dejan diez horas diarias para aportar un soplo de vida a esta guerra. En total más de 150 personas. “Muchos no se conocían y probablemente nunca se habrían conocido (en una fábrica de 15.000 empleados), pero ahora estamos todos unidos y comprometidos”, explica la directora de salud, seguridad y emergencias de Seat, Patricia Such.
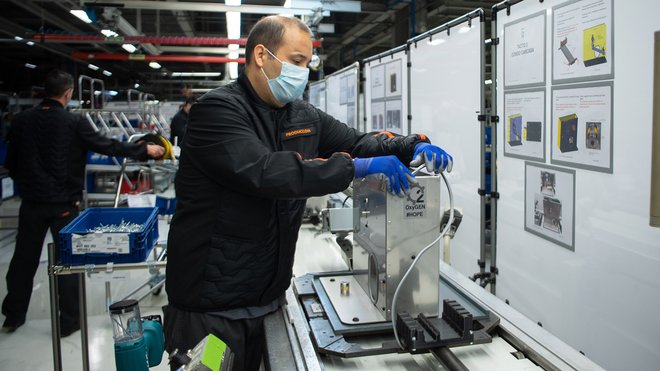
Homologación sanitaria
El ‘parto’ del respirador no fue fácil y tras una semana de batalla con los servicios de homologación sanitaria (toda el área legal de Seat trabajó intensamente) al final se consiguió. “Había que conseguir y demostrar que nuestro equipo no interfería en el funcionamiento de los equipos de las UCIS ni al revés, que los equipos de la UCI no interferían en el respirador”, señalan a pie de línea.
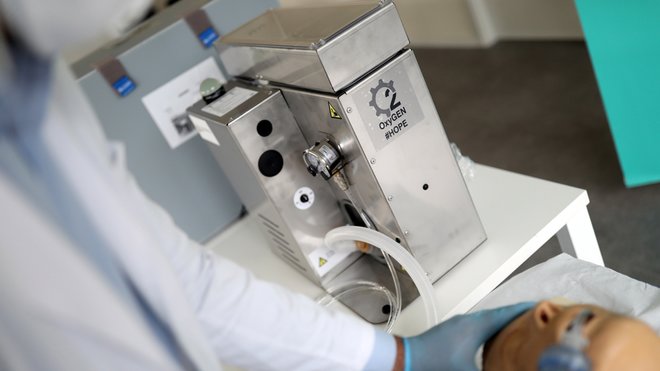
Valoraron las dos propuestas de respiradores que había (Protofy y Resistencia) y analizaron cuál era la idea más sencilla de escalar para poderlo producir en serie. “Combinamos el diseño del mismo con los materiales disponibles para fabricarlo. Muchas piezas son de la propia marca y desarrollados aquí (90%)”, otros como los motores de los limpiaparabrisas (con una pequeña modificación) son de proveedor Doga.
“Está claro que son respiradores de emergencia, de campaña y en ningún caso reemplazan por completo a los de las UCIS, son de apoyo en caso de necesidad si no hay”, comentan desde Seat. Es un modelo de tecnología abierta y la comparten de forma gratuita para todo el mundo. Seat no cobra nada por fabricarlos, ni tan siquiera se han puesto a saber qué cuestan. Simplemente se hacen. Además, ya han recibido muchas peticiones de información de Sudamérica (Chile, Ecuador o Colombia), Ucrania y desde Hungría.
Cómo se ha hecho
El Oxygen es un tipo de respirador de emergencia que no admite complicaciones. “Tomamos el feedback de los médicos que realmente son los clientes y eso hace que ajustemos los procesos de producción. Si una leva tiene que ir de una manera o de otra es importante, porque son los médicos los que los manipulan. Por ejemplo no tiene cierre de tapa para poder abrir y cerrar rápido. En caso de tener que hacerlo hay que dejar el mínimo de tiempo sin actuar el ventilador. También se pulen detalles y demás para que los sanitarios no se corten con los bordes por ejemplo, con un ventilador de aire caliente se modifican algunas piezas de forma manual”, nos explica el responsable de mantenimiento de Seat.
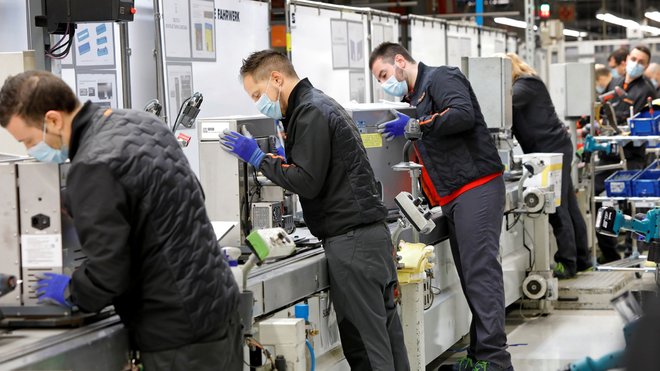
En el Taller 9 de Martorell hay una línea en la que se ensambla el subchasis delantero del León y es la que se ha ocupado. “Elegimos esa porque es flexible, manual y no requiere robotización. De hecho está pensado para que el respirador se puedan fabricar en cualquier factoría de coches del mundo porque las líneas son iguales. Al lado hay otra línea gemela que podría entrar en funcionamiento si hay que trasladarla por reinicio producción del León”, nos explican desde la zona de ensamblaje.
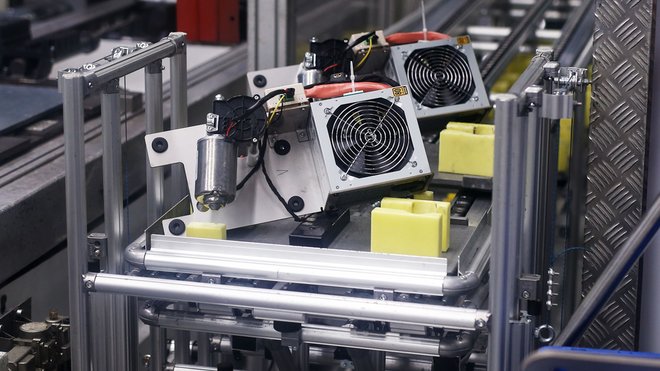
Casi 50 minutos de montaje
Todo el montaje es manual. Se van montando primero los motores con el cableado necesario, se emplean componentes fáciles de trabajar. Tiene el motor de limpiaparabrisas, piezas de resistencia como las que usan las lámparas de led y la fuente de energía de un PC (con su ventilador). “Esos son los componentes más importantes y hay que proveer stock para producción. Hay que tener plan B de proveedores en la recámara. Unos lo ceden gratis y otros no cobran el coste del material. Todo el mundo se ha implicado”, señalan.
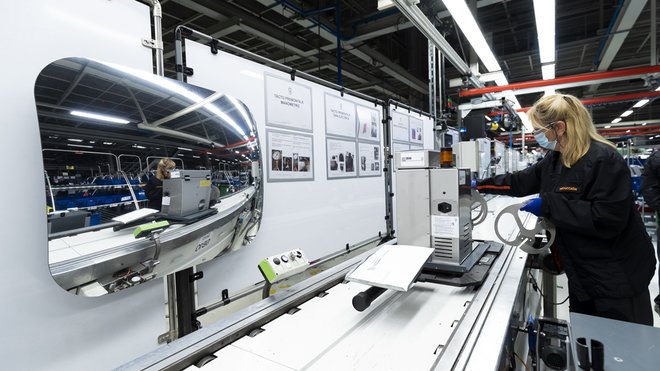
En estos momentos hay unos 400 acabados, unos 100 al día, y esperan que de aquí a este domingo ya estén con la producción diaria de 300 unidades que les ha pedido Sanidad. “Epodemos abastecer las necesidades de España y se puede pensar en hacerlos para donde se precisen”, comentan desde la dirección del proyecto.
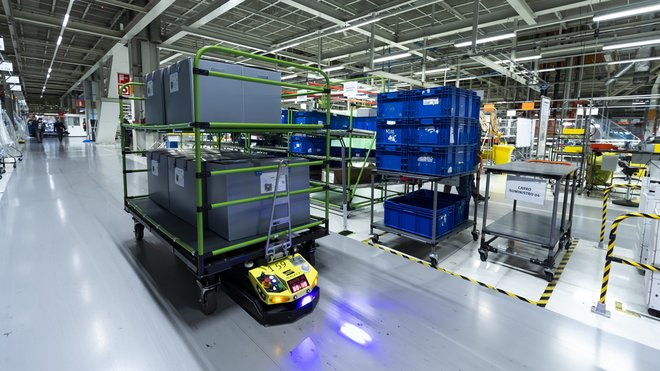
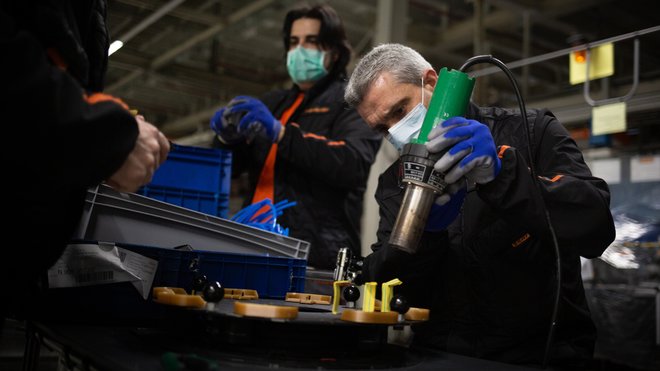
Una batalla difícil
Su i lusión por ayudar no cesará porque esta pandemia es algo muy grave. “Pienso que aprenderemos a valorar las cosas importantes en la vida. Jamás había pensado que lo que estudiaba en los libros de medicina sobre las pandemias podría ser real. Es un hecho que nos ha puesto delante las cosas más fundamentales de la vida. Hemos tenido que enfrentarnos, nos estamos enfrentando a algo que va más allá de lo imaginable. La verdad es que me ha impactado mucho”, explica la doctora Patricia Such.
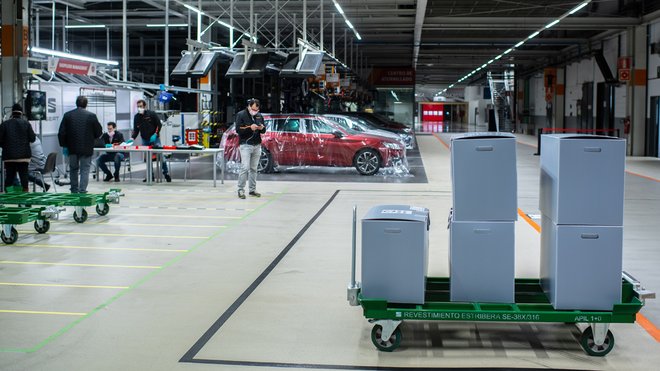
“Es impresionante ver como gente de diferentes especialidades dentro de la empresa, diferentes empleados y disciplinas que probablemente jamás se habrían visto en su vida, compartir un mismo proyecto en un corto espacio de tiempo, trabajar juntos por igual, con un volumen de energía asombroso. Hemos descubierto la faceta más humana de las relaciones personales en un momento en el que igual nos decían que la tecnología la estaba matando. Es una experiencia humana y emocional imposible de olvidar. Hemos demostrado que somos capaces de trabajar todos por igual, reaccionando en una respuesta automática ante la pandemia”, relata la responsable de los servicios médicos de Seat.
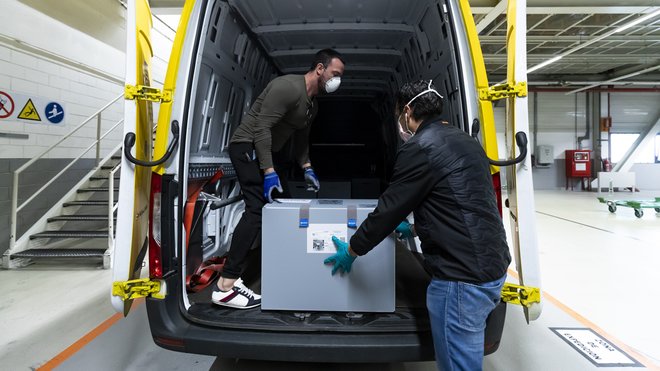
El resto de la fábrica está en silencio. Tampoco hay aplausos cada vez que sale un respirador de la línea. Eso solo se ve en las tomas de para la tele. Los trabajadores de Seat aplauden desde el corazón. “Aquí enviamos algo más de esperanza”, piensan en silencio.